How much time does the salt spray test correspond to the natural environment for one hour?
Many people have asked how long an hour of salt spray test is equivalent to the use of the site? Don't worry, let's first take a look at some of the principles and common problems of the salt spray test. The answer is published at the end of the article.
Salt spray corrosion principle
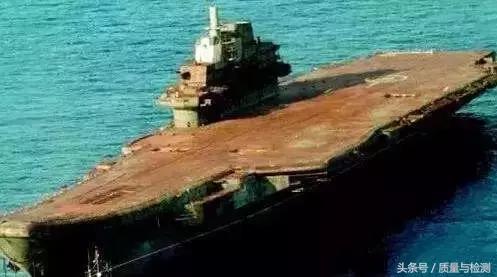
Most of the corrosion of metallic materials occurs in the atmosphere, which contains corrosive components and corrosive factors such as oxygen, humidity, temperature changes and pollutants. Salt spray corrosion is a common and most destructive atmospheric corrosion.
The corrosion of the metal material by the salt spray is mainly caused by the electrochemical reaction of the conductive salt solution into the metal to form a micro-battery system of "low-potential metal-electrolyte solution-high-potential impurity", electron transfer occurs, and the metal as the anode is dissolved. A new compound, the corrosive, is formed. The main function of the salt spray corrosion process is chloride ion. It has a strong penetrating power and easily penetrates the metal oxide layer into the metal to destroy the passive state of the metal. At the same time, the chloride ion has a small hydration energy. It is easily adsorbed on the metal surface and replaces the oxygen in the oxide layer of the protective metal to destroy the metal.
Salt spray corrosion test method and classification

Comparison before and after salt spray test
The salt spray test is an accelerated corrosion evalsuation method for an artificial atmosphere. It atomizes a certain concentration of salt water; it is sprayed in a closed incubator to reflect the corrosion resistance of the sample to be tested by observing the change of the sample to be placed in the box for a period of time. It is an accelerated test. The method has the salt concentration of the chloride in the salt spray environment, which is several times or several times of the salt spray content of the general natural environment, so that the corrosion rate is greatly improved, and the salt spray test is performed on the product, and the time for obtaining the result is also greatly shortened.
When testing a product sample in a natural environment, the corrosion time may take one year or even several years, and in a simulated simulated salt spray environment, similar results can be obtained in a few days or even hours.
The salt spray test is mainly divided into four types:
Neutral salt spray test (NSS);
Acetate spray test (AASS);
Copper accelerated acetate spray test (CASS);
Alternating salt spray test.
Comparison of four salt spray test methods in GB/T 10125
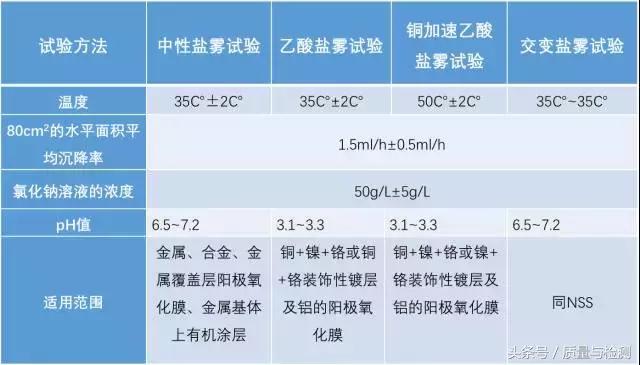
Salt spray corrosion test equipment

Salt spray corrosion test box structure diagram
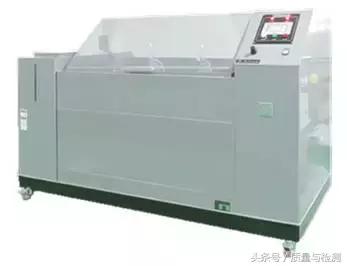
Salt spray corrosion equipment
evalsuation of salt spray test results
The method for assessing the results of the salt spray test includes:Rating method; corrosive appearance assessment method; weighing method.
Rating method
The percentage of the ratio of corrosion to total product is divided into several levels according to a certain method, and a certain level is used as a basis for qualification. It is suitable for evalsuation of flat samples. Such methods are used to evalsuate salt spray test results, such as GB/T6461-2002, ISO 10289-2001, ASTM B 537-70 (2013), and ASTM D 1654-2005.
Protection rating and appearance rating
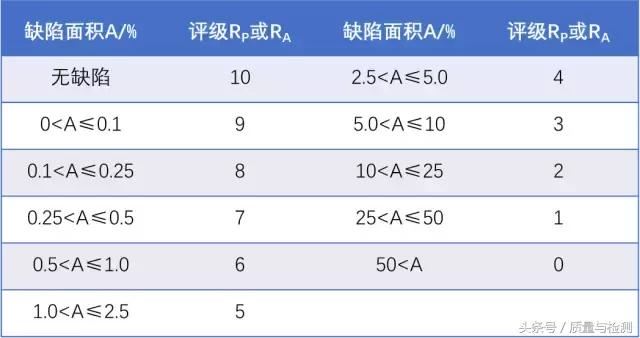
RP and RA values are calculated:

RP—Protection rating value;
RA—Appearance rating value;
A—When calculating RP, it is the percentage of the total area of the corrosion of the base metal; when calculating RA, it is the percentage of the total area of the corrosion of the protective layer.
Overlay classification and subjective evalsuation
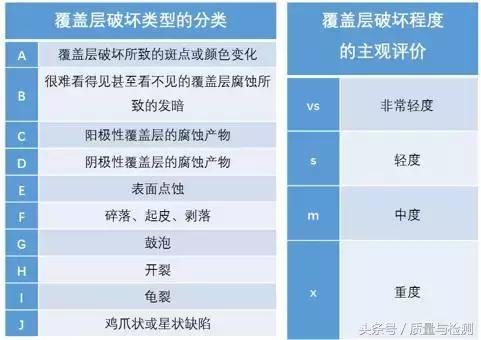
The protection rating is expressed as:RA/—
For example, if the slight rust exceeds 1% of the surface and is less than 2.5% of the surface, it is expressed as:5/—
The representation of the appearance rating is:—/RAValue + subjective evalsuation + overlay damage level
Such as: moderately spotted, the area is more than 20%, expressed as: —/2mA
The performance rating is expressed as:RAValue + subjective evalsuation + overlay damage level
For example, there is no corrosion of the base metal in the sample, but slight corrosion of the anodic cover layer less than 1% of the total area appears, which is expressed as 10/6sC.
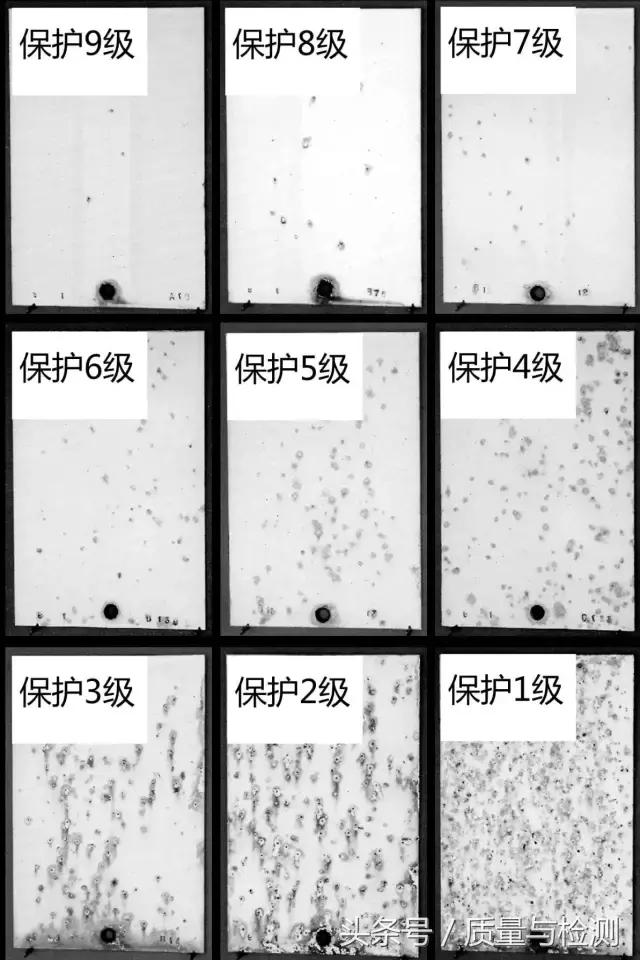
Photograph of the capping layer of the base metal (Source: ISO 10289-1999)
Corrosion appearance assessment method
It is a qualitative method for judging whether the product is corroded after the salt spray corrosion test. For example, JB4159-1999, GJB4.11-1983, and GB/T4288-2003 use this method to evalsuate the salt spray test results.
Corrosion characteristics of common plating parts after salt spray test
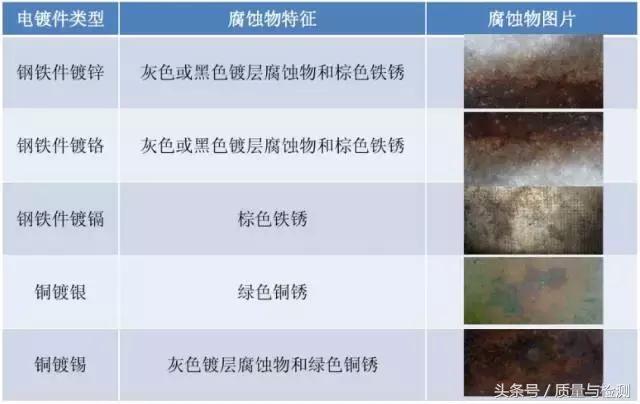
Weighing method
The weight of the corrosion loss is calculated by weighing the weight of the sample before and after the corrosion test to judge the corrosion resistance of the sample. It is especially suitable for assessing the corrosion resistance of a certain metal.
Corrosion rate calculation method:
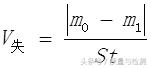
V失— Metal corrosion rate,g/m2·h;
m0 — Quality before corrosion of the test piece,g;
m1 — Quality before corrosion of the test piece,g;
S — Area of the test piece,m2;
t — Corrosion time of the test piece,h。
Factors affecting salt spray test
Test temperature and humidity
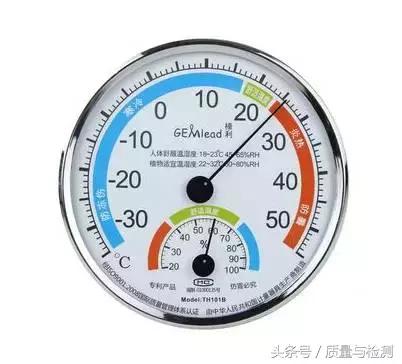
The critical relative humidity of metal corrosion is approximately 70%. When the relative humidity reaches or exceeds this critical humidity, the salt will deliquesce to form an electrolyte with good electrical conductivity. When the relative humidity is lowered, the concentration of the salt solution will increase until the crystalline salt is precipitated, and the corrosion rate is correspondingly lowered. As the temperature rises, the molecular motion increases and the high salt spray corrosion rate increases. The International Electrotechnical Commission pointed out that for every 10 °C increase in temperature, the corrosion rate is increased by 2 to 3 times, and the conductivity of the electrolyte is increased by 10 to 20%. For the neutral salt spray test, it is generally considered appropriate to select the test temperature at 35 °C.
Solution concentration
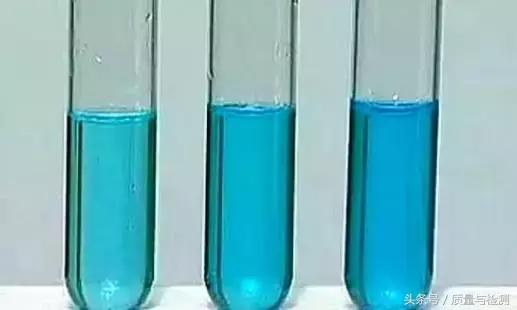
When the concentration is below 5%, the corrosion rate of steel, nickel and brass increases with the increase of concentration; when the concentration is more than 5%, the corrosion rate of these metals decreases with the increase of concentration. This is because, in the low concentration range, the oxygen content increases as the salt concentration increases; when the salt concentration increases to 5%, the oxygen content reaches a relative saturation, and if the salt concentration continues to increase, the oxygen content decreases accordingly. As the oxygen content decreases, the depolarization ability of oxygen also decreases, that is, the corrosion effect is weakened. For metals such as zinc, cadmium, and copper, the corrosion rate always increases as the concentration of the salt solution increases.
Sample placement angle
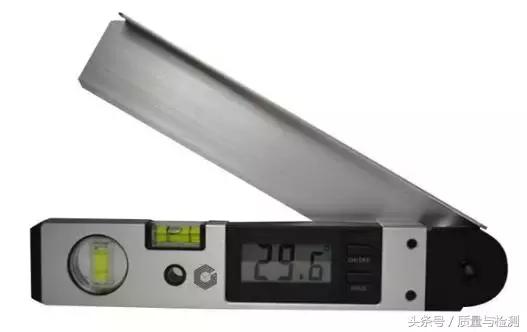
The sedimentation direction of the salt spray is close to the vertical direction. When the sample is placed horizontally, its projected area is the largest, and the sample surface receives the most salt spray, so the corrosion is the most serious. The results show that when the steel plate is at an angle of 45 degrees with the horizontal line, the weight loss per square meter is 250 g. When the plane of the steel plate is parallel to the vertical line, the weight loss of corrosion is 140 g per square meter. The GB/T 2423.17-93 standard stipulates that the flat sample should be placed at an angle of 30 degrees from the vertical.
pH value

The lower the pH, the higher the hydrogen ion concentration in the solution, and the stronger the acidity, the stronger the corrosion. The neutral salt spray test (NSS) has a pH of 6.5 to 7.2. The pH of the salt solution changes due to environmental factors. To this end, the salt spray test standard at home and abroad has specified the pH range of the salt solution, and the method of stabilizing the pH value of the salt solution during the test is proposed to improve the reproducibility of the salt spray test results.
Salt spray settlement and spray method
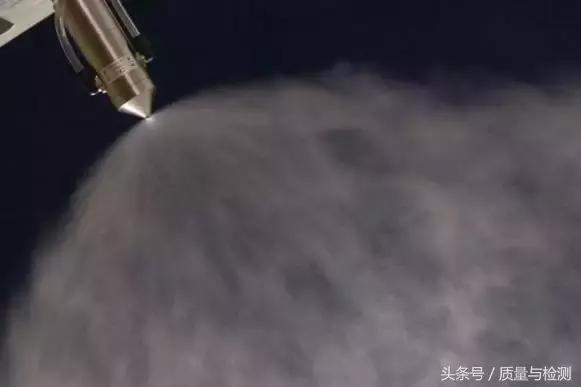
The finer the salt spray particles, the larger the surface area formed, and the more oxygen is adsorbed, the stronger the corrosion. Conventional spray methods include a gas jet method and a spray tower method. The most obvious disadvantage is that the uniformity of salt spray settlement is poor and the salt spray particle diameter is large. Different spray methods also have an effect on the pH of the salt solution.
Salt spray test related standards
Standard
standard name
GB/T 10125-2012
Artificial atmosphere corrosion test salt spray test
GB/T 12967.3-2008
Aluminium and aluminium alloys - Determination of anodic oxide film - Part 3: Copper accelerated acetate spray test (CASS test)
GB/ T6461-2002
Rating of samples and test pieces of metals and other inorganic coatings on metal substrates after corrosion tests
GB/T 2423.17-2008
Environmental testing of electric and electronic products - Part 2: Test methods Test Ka: salt spray
GB/T 2423.18-2012
Environmental test Part 2: Test method Test Kb: salt spray, alternating (sodium chloride solution)
JB 4159-1999
General technical requirements for tropical electrical products
GJB 4.11-1983
Marine electronic equipment environmental test salt spray test
ASTM B 117-2007
Standard Practice for Operating Salt Spray (Fog) Apparatus
ASTM B 368-2003
Standard Test Method for Copper-Accelerated Acetic Acid-Salt Spray (Fog) Testing
ASTM B 537-70 (2013)
Standard Practice for Ratingof Electroplated Panels Subjected to Atmospheric Exposure
ASTM D 1654-2005
Standard Test Method for evalsuation of Painted or Coated Speciments Subjected to Corrosive Environment
ASTM G 85 -2011
Standard Practice for Modified Salt Spray (Fog) Testing
How long does the salt spray test correspond to the natural environment for an hour?
The salt spray test is divided into two categories, one is the natural environmental exposure test, and the other is the artificial accelerated simulated salt spray environment test. The artificial simulated salt spray environment test uses a test equipment with a certain volume space—the salt spray test chamber, to artificially use the salt spray environment in the volume space to assess the salt spray corrosion resistance quality of the product. . Compared with the natural environment, the salt concentration of the chloride in the salt spray environment can be several times or several times higher than the salt spray content of the general natural environment, so that the corrosion rate is greatly improved, and the product is subjected to a salt spray test to obtain a result. The time is also greatly shortened. If a product sample is tested in a natural exposure environment, it may take 1 year to corrode, and in a simulated simulated salt spray environment, as long as 24 hours, similar results can be obtained.
The artificial simulated salt spray test includes a neutral salt spray test, an acetate spray test, a copper salt accelerated acetate spray test, and an alternating salt spray test.
(1) Neutral salt spray test (NSS test) is one of the earliest applications in the field of accelerated corrosion test. It uses a 5% aqueous solution of sodium chloride solution, and the pH of the solution is adjusted to a neutral range (6-7) as a solution for spraying. The test temperature is taken at 35 ° C, and the sedimentation rate of the salt spray is required to be between 1 and 2 ml / 80 cm 2 · h.
(2) The acetate spray test (ASS test) was developed on the basis of a neutral salt spray test. It is to add some glacial acetic acid to the 5% sodium chloride solution, the pH value of the solution is reduced to about 3, the solution becomes acidic, and the salt spray finally formed is also changed from neutral salt spray to acid. Its corrosion rate is about 3 times faster than the NSS test.
(3) Copper salt accelerated acetate spray test (CASS test) is a rapid salt spray corrosion test developed recently in foreign countries. The test temperature is 50 ° C. A small amount of copper salt - copper chloride is added to the salt solution to strongly induce corrosion. . Its corrosion rate is about 8 times that of the NSS test.
The specific time is converted to:
Neutral salt spray test 24h ⇌ natural environment 1 year
Acetate spray test 24h ⇌ natural environment 3 years
Copper salt accelerated acetate spray test 24h ⇌ natural environment 8 years